When people speak of identical twins, they’re usually referring to how the siblings look alike, with similar coloring and build, but look closely and you can see the subtle differences. Unlike people, in the machining world “identical” can have no subtle differences because the smallest imperfection, the tiniest scratch can change how a machine runs, how a product is built, or even how an end-user views the part.
We pride ourselves on assuring our customers that every part they get from us will be identical whether all from one lot with multiple runs, or if they come back time and time again for the same lot. Where other machine shops might just focus on the dimensional aspects of a part and ship a lot that meets the dimensions but a percentage of the parts don’t look like they were run in the same batch, that’s not how we do business. As we say, we live your parts, and if they don’t match that’s simply not acceptable. Call us perfectionists. We take that as a compliment.
From Start
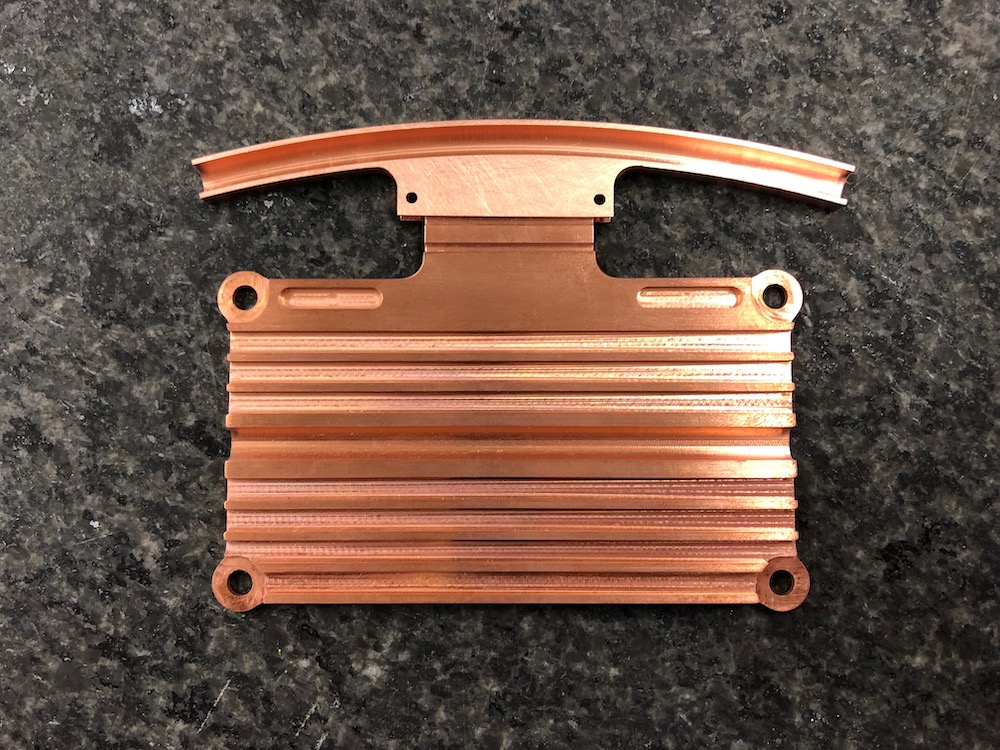
Being obsessed with the details is not easy, but we take on that role from the very start. When a customer sends us a drawing for the part they want, that covers the part features, materials and tolerances. We also prefer 3D models to support the prints. We receive orders that are focused on the quantity and release dates. Very few prints define exact instructions of the cosmetic requirements. We take it upon ourselves to make sure the parts not only conform to the print and tolerances, but are cosmetically excellent and identical. They have to look good!
The challenge is that most customers have a product line that requires a specific level of uniformity. The challenge is having a lot of people involved in the manufacturing process, a lot of hands touch each part. This process increases the chances for dings, scratches, or other flaws. If the process isn’t clean and organized, parts will get marked and inconsistencies will arise. We don’t allow that to happen.
To Finish
From initial programming to work holding and machining we are consistent and we maintain good surface finishes throughout the machining process. But it’s the steps we take in post-production that truly set us apart.
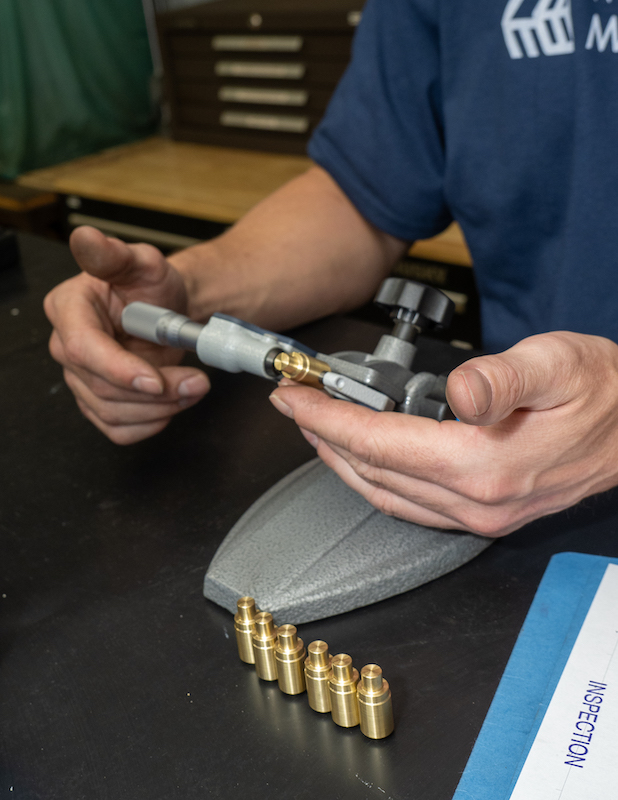
Parts go through a post-machining inspection and are deburred, and then inspected again. Next, the part typically goes to an outside process to get a type of plating, and then back again for another inspection. Following up with assembly, then one final inspection, and finally, we push it off to shipping. If you count that up, each part is inspected at least four times and along the way in our post production department. Our inspectors are trained in how to avoid adding marks, dings, or scuffs. The dimensional aspects of the part are examined to ensure they meet the dimensions per print, but we also make sure each part looks identical. If we find cosmetical issues along the way, that part gets pulled and reworked.For us, treating both the dimensional AND cosmetic aspects of your part as critical, and putting the effort forth to assure each is identical is just what we do. To find out how we can put our expertise to work for you, contact us or just submit your project here for a free quote.