While we remain your smalltown company, we are rapidly growing our capabilities to make more of what you need and make it much faster.
That’s why over the past several months we have purchased not one, but two Horizontal Machining Centers (HMC) that, working alongside our existing HMC department, will significantly ramp up our production capabilities. The HMC is the perfect machine for mass-producing a wide variety of metal products. It can do several types of machining on different product surfaces at one time, making it incredibly fast. In other words, it’s just perfect for us.
Boosting Productivity
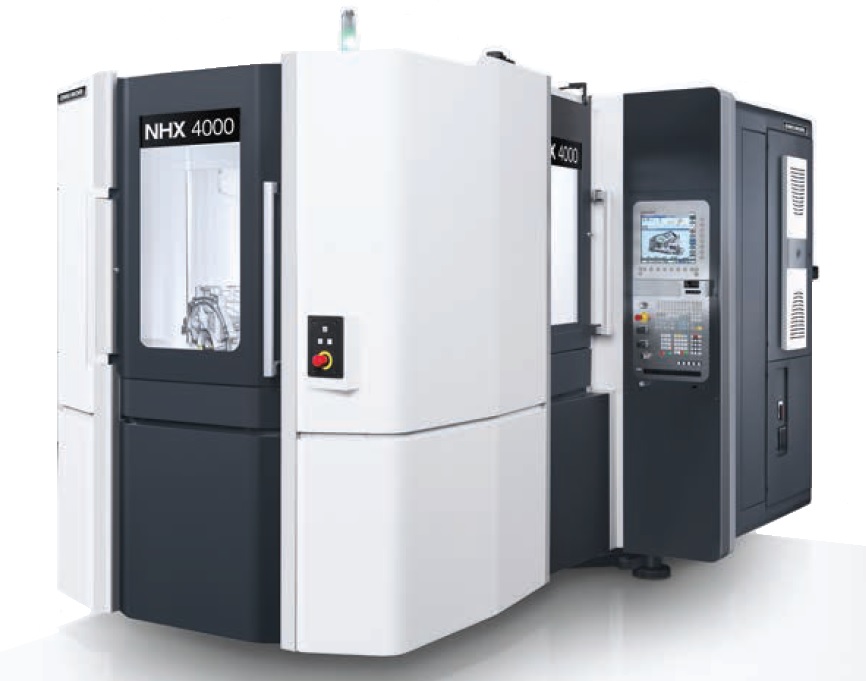
Our first buy was the Mori Seiki NH4000 DCG. Its DCG (Driven at the Center of Gravity) technology controls vibration to ensure precision, while the spindle that moves at a speed of 12,000 RPM boosts performance and produces a repeatable metal-removal rate among the highest available. The machine has full 4-axis capabilities allowing parts to rotate on the table while the cutter is engaged so we can do full-contour cuts, or we can rotate to any degree and machine on that plane. That’s versatility.
Next up, we bought the Mori Seiki NHX4000 that again brings high speed and high precision machining with its speedMASTER spindle, rigid bed, and all the other components of the NH4000. Together these HMC’s give us improved technology and automation, as well as faster processing. They allow for many configurations so we can handle even more types of jobs including those with very complex shapes. And because these machines can basically run with just minimal supervision 24/7, our work never stops.
Better Together
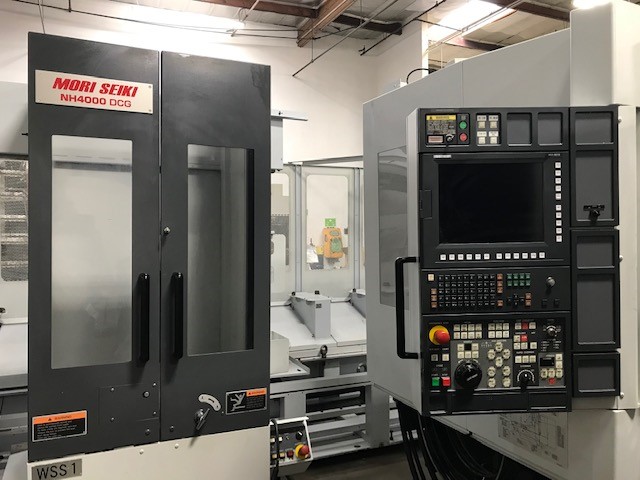
Both HMC’s have ATC Systems that hold 60 to 120 tools, a far cry from the 20 to 40 found in other machining centers. That combined with its part probing and tool breakage detection skyrockets our production capabilities. With tools already in place, our set-up time is decreased. Almost magically, if a tool breaks the machine pulls out a replacement to finish the job and sends us an alert that a replacement will be needed. Faulty tools or different tools between jobs no longer have to be manually changed. These high-level technological advances mean our speed and efficiency in jumping from one job to another greatly increases while downtime in replacing parts decreases– a win-win for our customers.
Our new additions provide us with flexibility, great precision, and even higher levels of accuracy, and our team is excited to get their hands on these new toys to see what they can do. We’re also thrilled by all the benefits these machines can bring to you. As our customers challenge us with higher and higher quantity orders and more complex designs we can now confidently say we are ready.